Blog post
Armored vehicles, whether wheeled or tracked, serve a variety of different functions on the battlefield: as reconnaissance, ambulance, infantry delivery vehicles. Sixty years ago, the U.S. military started using armored personnel carriers with aluminium plate. One of the first of these was the M113, a true workhorse that provided speed, agility, and safety during the Vietnam War. Aluminium made the M113 lighter than previous military vehicles yet still strong enough to protect its crew and passengers.
Quicker and stealthier with aluminium
Over the past decade aluminium armor plates have become increasingly common in military vehicles thanks to their combination of strength and low density. Aluminium’s lighter weight may be used to improve vehicle speed and cross-country mobility compared to steel hulled vehicles with the same level of protection. Better mobility allows for greater responsiveness in battle and more maneuverability. These features combine to lower a vehicle’s vulnerability and improve its occupants’ survivability.
Lighter weight reduces fuel consumption, increases operational range, and allows access to more of the battlefield than heavier vehicles due to weight limitations along roads and bridges. Lighter vehicles mean less fuel is required, reducing logistical burdens. This lower weight also increases the number of vehicles that can be carried into remote areas by air, allowing commanders to rapidly concentrate the forces they need with more aircraft available to carry supplies and ammunition.
Increased threats require higher performance
Aluminium armored plate is applied to two different areas of military vehicles: perimeter armor (sides and top) and the underbelly. Although both applications are designed to protect soldiers from enemy fire on the battlefield, they have very different performance requirements. Perimeter armor is designed to stop the penetration of ballistic rounds from enemy fire, normally using a harder aluminium alloy/temper combination. Underbelly plate protects against blasts from mines and Improvised Explosive Devices (IEDs), which are designed to detonate under moving vehicles on roads. The underbelly plate alloy is able to deform without breaking or cracking to protect the vehicle occupants.
As weapons of war become more sophisticated, threat levels are also increasing. Soldiers find themselves fighting against threats fired at close distance. In response to these new threats, the military requires even higher-performance aluminium armor alloys to protect a vehicle’s crew and occupants from blast, projectiles, fragments, and armor piercing weapons.
Constellium, working with the Army Combat Capabilities Development Command (CCDC) Army Research Laboratory (ARL) and the CCDC Ground Vehicle Systems Center (GVSC), is developing the next generation alloys for specific applications. The United States Department of Defense (DoD) has given Constellium’s Ravenswood, West Virginia plant several grants to support its defense production. “The last 10 – 12 years have seen this relationship mature into a true partnership,” says Buddy Stemple, CEO Constellium Rolled Products Ravenswood.
Aluminium alloy 5083-H131 has traditionally been the top choice for military armor plate. Constellium Ravenswood recently concluded a two-year project with the DoD, the U.S. Army Research Laboratory (ARL), and other partners to produce heavier gauge 5083 armor applications. These efforts allow Constellium to produce plates with thickness from 3 inches to 10.5 inches. These thicker plates are changing the design and fabrication of combat vehicles and allow the production of large single-piece components to improve hull strength and durability compared to traditional welding of multiple small plates into larger assemblies. Single-piece components may cost more to procure than individual plates, but are cost competitive once costs associated with welding, grinding, distortion mitigation, and inspections are considered. Single-piece components reduce hull fabrication time on the assembly line and ultimately build a stronger vehicle.
A 2018 Interagency Task Force report identified cold rolled aluminium plate as “essential for armoring U.S. ground combat vehicles, constructing Navy ships, and building military aircraft.” Ravenswood is one of two remaining plants in the U.S. that has the capability to cold roll aluminium plate. Cold rolling is a stage of the manufacturing process in which aluminium plate is compressed and elongated to improve plate flatness, outer surface appearance characteristics, reduce internal stresses, and strengthen 5xxx series alloys. Ravenswood’s cold mill is an important producer of armored plates and blast protection kits for tactical wheeled vehicles.
The U.S. Assistant Secretary of the Army for Acquisition, Logistics, and Technology has directed effort and resources to assist Constellium in the development of the thick plates’ capability, including investments at Ravenswood to cold work up to 10.5-inch plate. Constellium and Army personnel work closely on a regular basis, to develop advanced alloys and manufacturing processes. The close cooperation between the Army and Constellium has been key in efforts to provide improved protection for defense vehicles.
New alloys rise to the occasion
In the past few years, a number of new and more advanced alloys have been developed. These include Constellium’s proprietary 2139 and 7056 alloys, which stand out for their combination of blast performance, armor piercing protection, formability, and corrosion resistance. Corrosion resistance is a key requirement for military vehicles that operate many different environments from the ocean shore to high deserts. Both alloys have their origins in aerospace applications and are now finding places in ground vehicles.
A U.S. Army prototype vehicle, called the Concept for Advanced Military Explosion-mitigating Land (CAMEL), was built using 2139 alloy. It was successfully tested in a variety of threat scenarios. The material performed so well it was sent back to the range on multiple occasions, increasing the blast level above the requirement until a breach finally occurred. The vehicle with 2139 alloy plate outperformed the blast mitigation objective by a significant margin. Another application of 2139 alloy was a U.S. Special Operations Command (SOCOM) need for weight reduction without giving up underbelly protection. In choosing 2139 alloy plate, SOCOM reduced the weight on its MRAP All-Terrain Vehicle (M-ATV) by approximately 1,200 lbs.
Partnering with the U.S. department of defense to stay ahead of the curve
The Covid-19 pandemic has shown that it is critical for all industries – especially defense – to be autonomous and able to rely on domestic producers.
Constellium’s plant in Ravenswood, West Virginia has supplied the U.S. Department of Defense (DoD) with a large portfolio of rolled aluminium products for decades, and continues to do so today.
On November 8, 2021, the Ravenswood plant is cutting the ribbon on its upgraded 144” cold mill, thanks in large part to a grant from the Department of Defense. With this investment, Ravenswood was able to upgrade the 144’’ mill, resulting in significant increases in throughput to meet the DoD’s growing requirements for cold rolled aluminium. This upgrade enables the DoD-Constellium team to develop, prototype, and implement manufacturing processes for a new generation of armored products. Constellium will continue to provide our women and men in uniform the most advanced and highest performing aluminium for their vehicles, ships, aircraft, and equipment.
“Without this rebuild, Constellium would not have been able to provide enough material in the event of a surge requirement for multiple alloys, which are critical to our national defense,” said Buddy Stemple.
Blast test on Constellium’s armored plate:
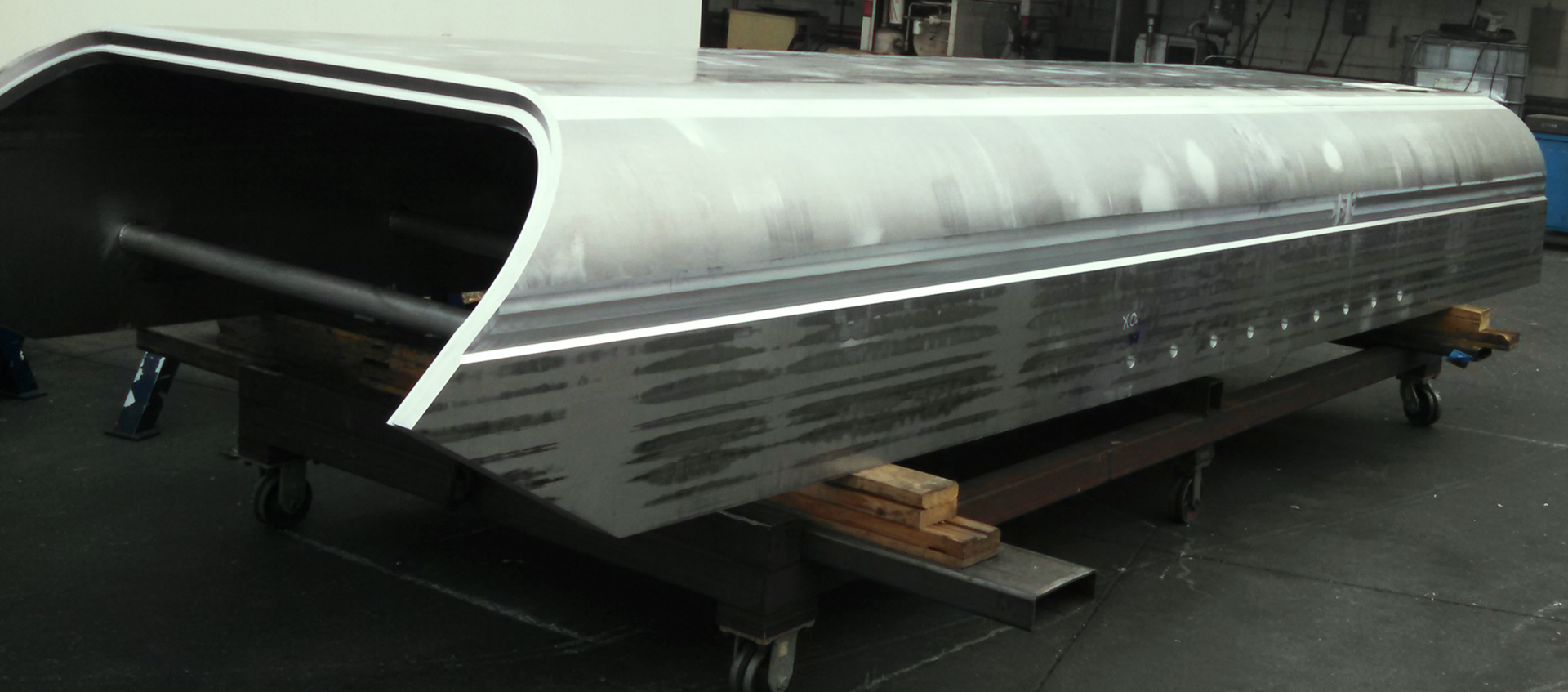
6" thick, bump formed, 7xxx series plate; single piece configuration
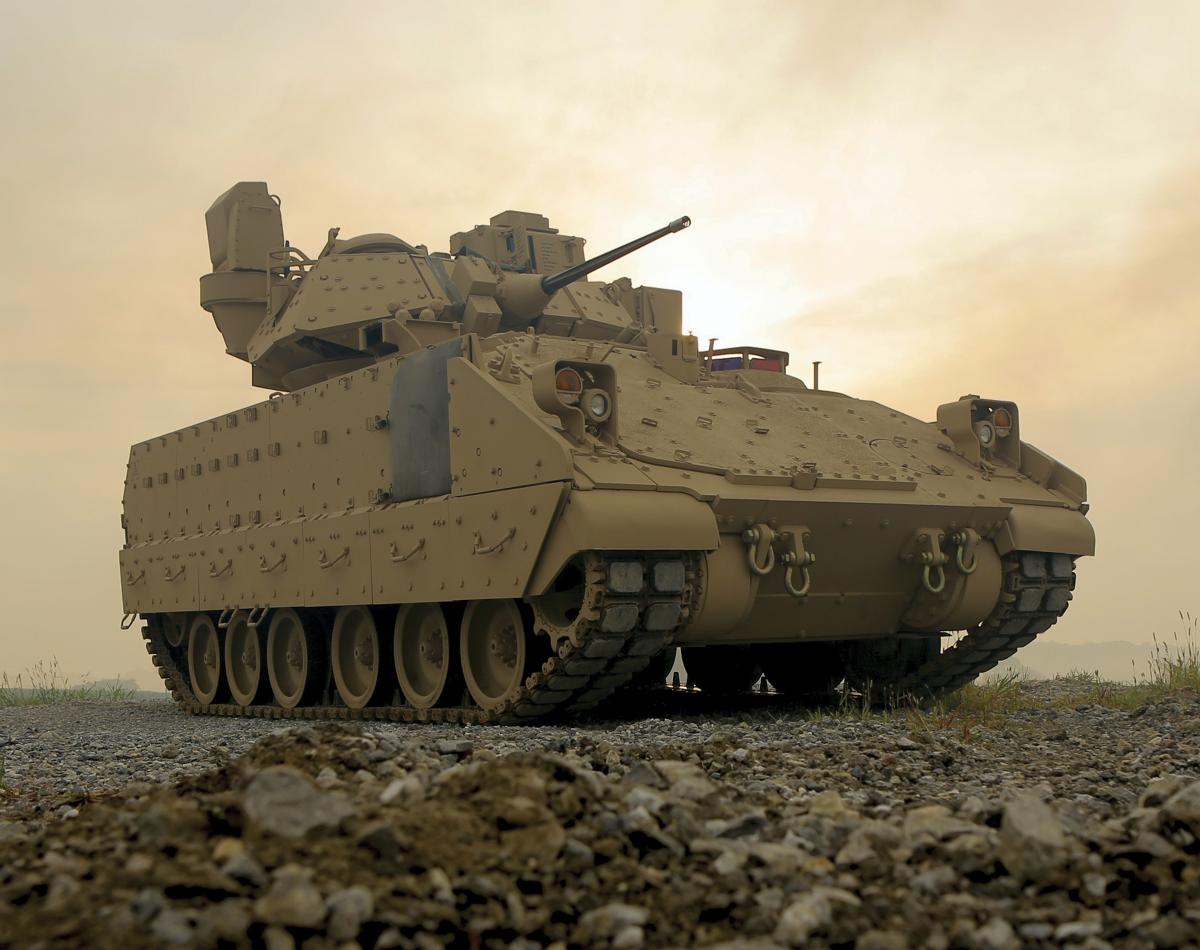